スマートファクトリーとは?意味やメリット、課題やIoTの活用事例を紹介
スマートファクトリーとは?意味やメリット、課題やIoTの活用事例を紹介
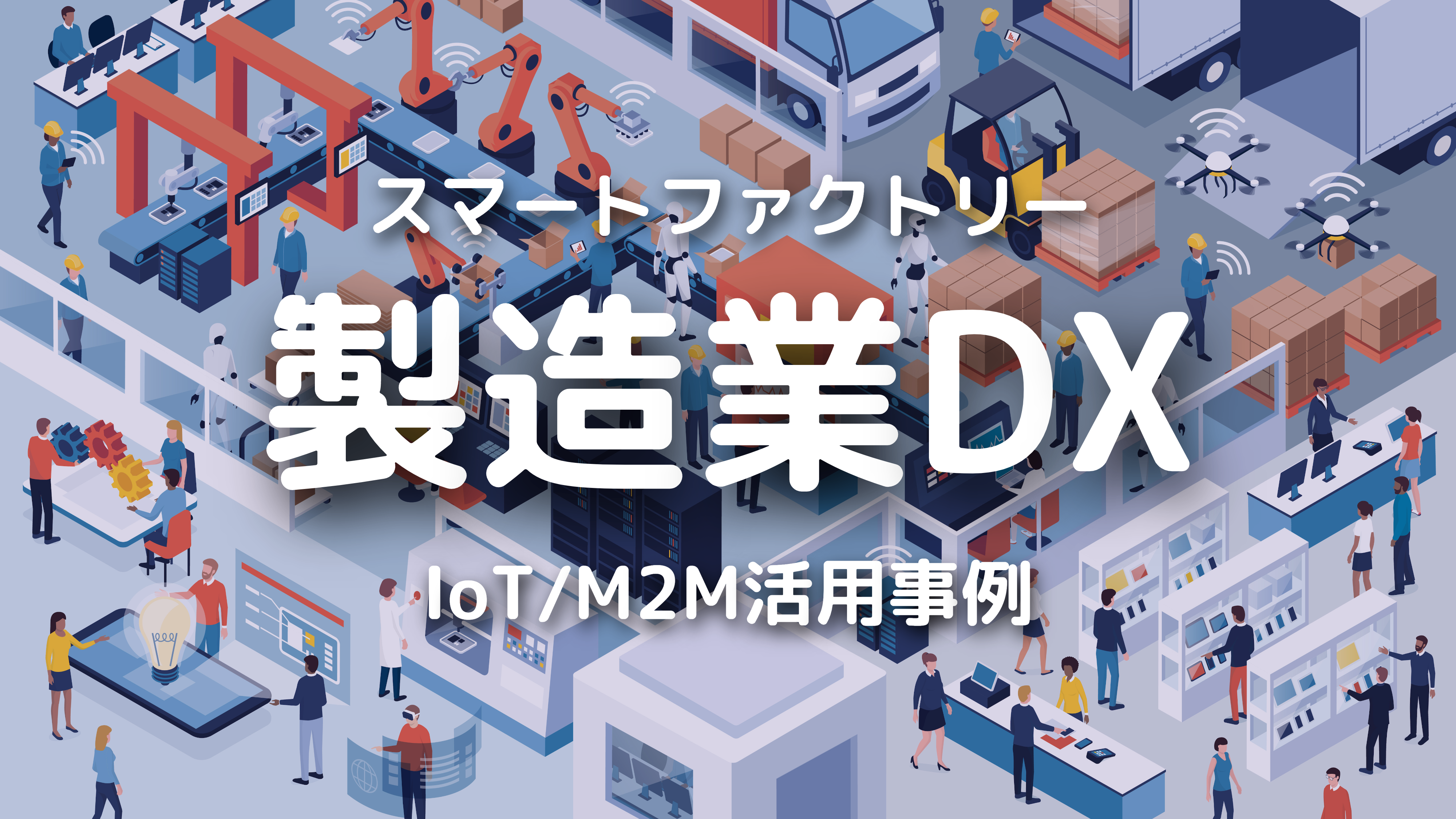
近年、さまざまな業界で注目を集めているのは、デジタルトランスフォーメーション(DX)による組織改革や事業改革です。製造業も同様に、IoTやM2Mの活用によるスマートファクトリーへの移行が進んでいます。 製造業におけるIoTやM2Mの活用、つまりスマートファクトリーは、5G時代、AI時代、IoT時代に生き残るためには不可欠な施策です。しかし、コストやリソースの制約から、まだこれらの技術を導入できていない企業も少なくありません。この記事では、製造業におけるIoT・M2Mの導入の意義やメリットについて紹介します。
目次
製造業が抱える3つの課題
スマートファクトリーの紹介の前に、現在、製造業が抱えている大きな3つの課題を紹介します。
VUCA時代への突入
製造業が抱える3つの課題の1つ目は、VUCA時代への突入です。
VUCAとは、「Volatility(変動性)」「Uncertainty(不確実性)」「Complexity(複雑性)」「Ambiguity(曖昧性)」の頭文字を取った造語で、社会やビジネスにとって、未来の予測が難しくなる状況のことを意味します。
Volatility(変動性)の影響
Volatility(変動性)とは、テクノロジーの進化や価値観、社会の仕組み、顧客ニーズの変化のことを指します。まさに、ほんの10数年の間にITやICT、さらには、IoT、AI、5Gなどテクノロジーの急速な進化によって、価値観や社会の仕組み、顧客ニーズが大きく変化しました。
Uncertainty(不確実性)の影響
Uncertainty(不確実性)とは、自然環境や政治・国家、制度などの不確実さを指します。まさに、新型コロナウイルスにより、人々の生活様式の変化が起きました。さらには、ロシアのウクライナ侵攻のような世界中での政治や国家体制などにも変化が生じています。
Complexity(複雑性)の影響
Complexity(複雑性)とは、これまでの日本国内だけのビジネス展開ではなく、グローバルでのビジネス展開により世界各国の情勢や政治体制、法律、文化などにも着目し、ビジネス展開を図らなければいけない状態になりました。これからもより一層、複雑性が増していくはずです。
Ambiguity(曖昧性)の影響
Ambiguity(曖昧性)とは、上記3つの「Volatility(変動性)の影響」「Uncertainty(不確実性)の影響」「Complexity(複雑性)の影響」の様々な要素が組み合わさることで、前例のない出来事が多発し、より一層、曖昧性の高い世界になっていくということです。
労働力の不足
製造業が抱える3つの課題の2つ目は、労働力の不足です。
「ジャパン・アズ・ナンバーワン」と呼ばれた戦後の日本経済の高度経済成長期には、製造業には多くの人材がいましたが、2000年代に入り、34歳以下の若年就労者が徐々に減り始め、今では、製造業の多くが継承者不足と組織の高齢化に悩まされています。
デジタルシフトへの遅れ
製造業が抱える3つの課題の3つ目は、デジタルシフトへの遅れです。
工場内にAIやIoTを導入して、あらゆる機器をインターネットに接続し、デジタルデータを活用することで、品質や生産性の向上、作業の自動化・見える化などを実現することが目的のスマートファクトリーですが、経済産業省が2020年に公表した『2020年版ものづくり白書』によると、「デジタル技術を活用している」と回答した企業は49.3%である一方で、「未活用(活用を検討中、活用していない、無回答)」と回答した企業も46.4%となり、製造業では、二極化が進んでいます。
(参考)2020年版ものづくり白書(PDF版)|経済産業省
スマートファクトリーとは?
製造業界が抱える課題を踏まえ、次にスマートファクトリーについて紹介します。
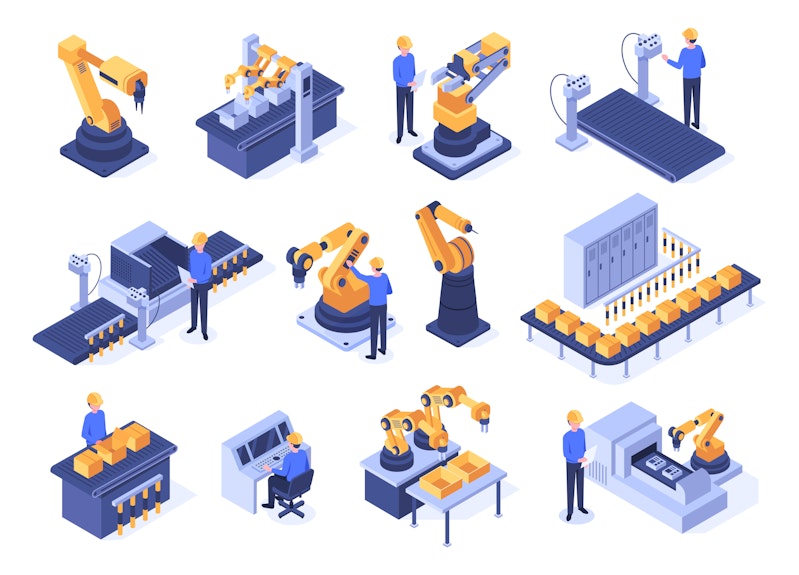
スマートファクトリーの意味
スマートファクトリーとは、IoTやAI、ICT、ロボットなどのデジタル技術を活用し、工場全体がDX(デジタルトランスフォーメーション)された状態の工場のことを言います。
具体的には、スマートファクトリーでは、IoT(モノのインターネット)やM2Mの活用により、様々なデバイスをインターネットに接続し、それぞれの機器や機械を自動的に遠隔操作したりすることができます。
その他にも、生産性が高くなるように、IoTやM2Mデバイスから収集された情報をもとに、AI分析をすることで、最適な生産活動ができるように改善をするということも可能です。
「IoT」について詳しく知りたい方は、こちらの記事もご覧ください。
『IoTとは?Internet of Things(モノのインターネット)の意味や仕組みを事例を交えてわかりやすく簡単に解説!』
「M2M」について詳しく知りたい方は、こちらの記事もご覧ください。
『M2M(Machine to Machine)とは?意味や仕組み、IoTとの違い、事例を簡単に紹介!』
「IT・ICT・IoTの違い」について詳しく知りたい方は、こちらの記事もご覧ください。
『IT・ICT・IoTの違いとは?それぞれの意味や活用事例を紹介!』
スマートファクトリーの背景
「スマートファクトリー」という概念や言葉に注目が集まった背景には、インダストリー4.0(Industry4.0 / 第四次産業革命)が関係しています。
このインダストリー4.0(Industry4.0 / 第四次産業革命)は、ドイツが2011年に『2020年に向けたハイテク戦略の実行計画』の中で示した10施策のうちの1つとして掲げられた構想です。同時期に、アメリカでも同様に、インダストリアル・インターネット・コンソーシアム(IIC)という構想を打ち出しています。
このインダストリー4.0の中で示されている、未来の工場の姿である「スマートファクトリー」という姿が、日本では大きな注目を集めました。つまり、製造業では、インダストリー4.0という目標へ向かって、スマートファクトリーの実現を目指しているということです。
(参考)インダストリー4.0とは|総務省
スマートファクトリーの目的
日本の経済産業省が2017年5月に公表した『「 スマートファクトリーロードマップ 」〜 第4次産業革命に対応したものづくりの実現に向けて 〜』によると、スマートファクトリーには、大きく7つの目的があります。
①品質の向上
②コストの削減
③生産性の向上
④製品化・量産化の期間短縮
⑤人材不足・育成への対応
⑥新たな付加価値の提供・提供価値の向上
⑦その他
さらに、7つの目的を達成しているかを測るレベル分けを「スマート化のレベル」という形で3段階で行なっています。
レベル1:データの収集・蓄積
レベル2:データによる分析・予測
レベル3:データによる制御・最適化
ここからは、スマートファクトリーの7つの目的とそれぞれ3つのレベルについて紹介します。
(参考)スマートファクトリーロードマップ 」〜 第4次産業⾰命に対応したものづくりの実現に向けて 〜|経済産業省
①品質の向上
1つ目の目的は、「品質の向上」です。
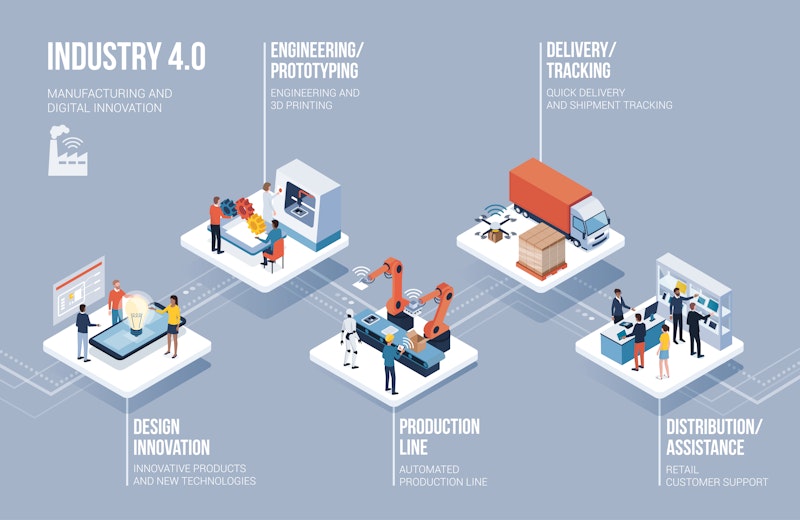
スマートファクトリー化の目的 | レベル1(データの収集・蓄積) | レベル2(データによる分析・予測) | レベル3(データによる制御・最適化) | 対象企業層 | スマート化の対象プロセス |
---|---|---|---|---|---|
(1)不良率の低減 | 人の作業内容(作業⼿順や作業結果など)をセンシングすることで、作業内容を収集・把握できる。ポカミスが発⽣した際、人へ早期に通知できる。 | 過去のポカミスを分析することで、ポカミスが発⽣しやすい作業⼯程を特定できる。 | 分析結果に基づいて、従業員を⼈材育成したり、設計を変更することで、ポカミスの発⽣を抑制し、不良率を削減・最⼩化できる。 | ・素形材加工企業・設備・金型供給企業・組み立て企業 | ・製品企画、 開発・設計 |
(2)品質の安定化、ばらつきの低減 | 設備にセンサを取り付けて搭載してモニタリングすることで、加⼯⼨法などの製品の品質データと設備の加⼯条件・設定値を収集・把握できる。各従業員の作業状況(作業動線、作業時間、作業内容など)をセンシングすることで、各従業員の作業状況を収集・把握できる。 | 収集したデータを分析し、品質のばらつきの要因を特定することで、加⼯誤差や加⼯性能の改善につながる加⼯条件・設定値をモデル化できる。収集したデータを分析し、作業のばらつきの要因を特定することで、作業の改善につながる作業条件をモデル化できる。 | 構築した加⼯改善モデルを⽤いて、設備の加⼯条件・設定値を最適化することで、加⼯誤差を最⼩化したり、加⼯性能を最⼤化できる。構築した作業改善モデルを⽤いて、作業状況を改善、均⼀化することで、作業のばらつきを最⼩化できる。 | ・素形材加工企業・設備・金型供給企業・組み立て企業 | ・製品企画、 開発・設計・生産 |
(3)設計品質の向上 | 製品にセンサ・通信機能を搭載することで、製品の使⽤状況や使⽤環境のデータを収集・把握できる。 | 収集したデータと設計データとを関連付けて因果関係を明らかにすることで、品質・信頼性の向上につながる設計仕様・⽣産⽅法を分析できる。 | 構築した作業改善モデルを⽤いて、作業状況を改善、均⼀化することで、作業のばらつきを最⼩化できる。 | ・素形材加工企業・設備・金型供給企業・組み立て企業 | ・生産 |
(1)不良率の低減
まず最初に、不良率の削減に向けた重要なステップは、IoTセンサーなどを活用して人々の作業手順と結果を収集することです。これにより、作業のログを記録し、人為的なミスが発生した場合には迅速に通知が行えるようになります。
さらに、AIなどを用いて過去の人為的ミスを分析し、これらを未然に防ぐための環境整備を行うことが重要です。最終的には、AI分析に基づいた作業データを活用して、人材育成と設備設計を行い、不良率の低減を目指す必要があります。
(2)品質の安定化、ばらつきの低減
品質の確保とばらつきの低減に関して、重要なのは、IoTセンサーを設備に導入し、生産工程の品質データや設備の条件と設定値を監視できるようにすることです。
また、IoTセンサーから収集されたデータを分析し、品質のばらつき要因を特定し、生産条件や設定値の最適化につなげることが必要です。最終的には、生産プロセスの最適化に向けてモデルを活用し、加工誤差を最小化し、生産性を最大化することを目指すべきです。
作業者の作業のばらつきを最小化するためには、各従業員の作業状況(作業フロー、作業時間、作業内容など)をIoTセンサーなどを通じて収集し、従業員の作業状況を把握する環境を整えることが重要です。
さらに、IoTセンサーから得られたデータを分析し、作業のばらつきの要因を特定し、作業条件のモデル化に取り組むことが重要です。最終的には、作業プロセスの改善に関するモデルを活用して、作業の改善と均一化を実現し、作業のばらつきを最小限に抑える必要があります。
(3)設計品質の向上
製品や装置の設計品質を向上させるためには、まずIoTセンサーや通信機能を導入して、製品や装置の使用状況と環境データを収集し、これらを活用できるようにすることが不可欠です。
さらに、収集されたデータと設計データを結びつけ、因果関係を明らかにし、品質と信頼性を向上させるための設計仕様と生産方法を分析できるようにする必要があります。最終的には、これらの分析結果に基づいて設計仕様と生産方法を修正・改善し、製品や装置の品質と信頼性を向上させるべきです。
②コストの削減
2つ目の目的は、「コストの削減」です。
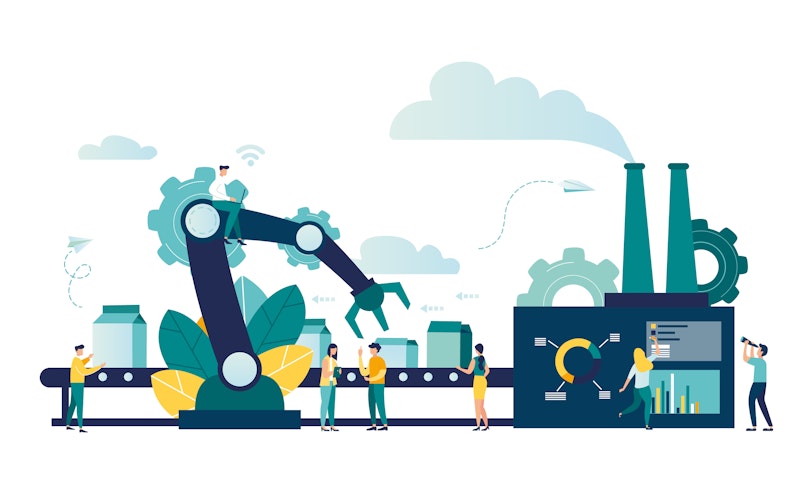
スマートファクトリー化の目的 | レベル1(データの収集・蓄積) | レベル2(データによる分析・予測) | レベル3(データによる制御・最適化) | 対象企業層 | スマート化の対象プロセス |
---|---|---|---|---|---|
(1)材料の使用量の削減 | 設計事例を収集してデータベースとして蓄積することで、過去の事例を容易に参照できる。解析・シミュレーションソフトウェアを利⽤することで、構造等を解析できる。 | 過去の設計事例の分析や、解析・シミュレーションソフトウェアなどによって、材料の軽量化や部品点数の削減につながる形状・構造等を知⾒としてモデル化できる。 | 構築した設計改善モデルを⽤いて、製品設計を最適化することで、材料の使⽤量を最⼩化できる。 | ・素形材加工企業・設備・金型供給企業・組み立て企業 | ・製品企画、 開発・設計 |
(2)生産のためのリソースの削減 | MES(製造実⾏システム)などの⽣産管理システムのデータを利⽤することで、⽣産の作業プロセスの進捗状況や、人(⼯数)、材料、エネルギーの投⼊状況を収集・把握できる。 | ⽣産の作業プロセスの進捗状況を踏まえて、人(⼯数)、材料、エネルギーの予定投⼊量、予定⽣産量などを予測できる。 | 設備の稼動計画、人の作業計画を修正・最適化することで、投⼊する人(⼯数)、材料、エネルギーを最⼩化できる。 | ・素形材加工企業・設備・金型供給企業・組み立て企業 | ・生産 |
(3)在庫の削減 | MES(製造実⾏システム)などの⽣産管理システムのデータを利⽤することで、⽣産計画や⽣産実績データの⼊⼒・表⽰・確認が容易にできる。 | 受注、⽣産、出荷の計画・実績データを連動させて分析することで、需給変動要因を明らかにしたり、需給を予測できる。 | 需給予測に基づいて、調達した資材や⽣産した製品の在庫が最⼩化となるよう、⽣産計画・出荷計画の作成を⾃動化・最適化できる。 | ・素形材加工企業・設備・金型供給企業・組み立て企業 | ・受注・調達・⽣産・物流・販売 |
(4)設備の管理・状況把握の省力化 | 設備にセンサを取り付けてモニタリングすることで、設備の設置場所にいなくても、複数の設備の稼働状況を、遠隔でリアルタイムに収集・監視できる。 | - | 設備に異常などが発⽣したときに、従業員への通知を⾃動化することで、監視・点検の管理⼯数を最⼩化できる。 | ・素形材加工企業・設備・金型供給企業・組み立て企業 | ・⽣産 |
(1)材料の使用量の削減
最初に、過去の設計事例を収集し、データベースに整理・保管して、これらの情報に迅速にアクセスできるようにすることが不可欠です。これにより、構造などの分析と解析が簡単に行えます。
また、過去の設計事例を分析し、材料の軽量化や部品の最適化に関連する形状や構造をモデル化できるように努力することが大切です。
最終的には、設計改善モデルを活用して、製品設計を最適化し、材料の使用量を最小限に抑えることが重要です。
(2)生産のためのリソースの削減
生産プロセスの進行状況やリソース(人員、材料、エネルギー)の使用状況を把握するために、最初に製造実行システム(MES)などの生産管理システムのデータを活用することが必要です。これにより、生産プロセスの進行状況を把握し、リソースの予定使用量や予定生産量を予測できるようになります。
最終的には、設備の運用計画と作業スケジュールを調整し、リソースの最適な利用を実現することが重要です。
(3)在庫の削減
製造実行システム(MES)などの生産管理システムのデータを活用し、生産計画や生産実績データの入力と表示を簡素化することが初めに必要です。また、受注、生産、出荷の計画と実績データを連携して分析し、需給変動の要因を特定し、需給を予測することが大切です。
最終的には、需給の予測に基づいて、資材の調達と製品の在庫を最小限に抑えるために、生産計画と出荷計画を自動化し、最適化することが重要です。
(4)設備の管理・状況把握の省力化
最初に、IoTセンサーを設備に取り付け、リアルタイムで遠隔から複数の設備の稼働状況をモニタリングできるようにすることが必要です。また、設備に異常が発生した場合、従業員へ自動通知を送る仕組みを整備し、監視と点検の手間を最小限に抑えることが重要です。
③生産性の向上
3つ目の目的は、「生産性の向上」です。

スマートファクトリー化の目的 | レベル1(データの収集・蓄積) | レベル2(データによる分析・予測) | レベル3(データによる制御・最適化) | 対象企業層 | スマート化の対象プロセス |
---|---|---|---|---|---|
(1)設備・人の稼働率の向上 | MES(製造実⾏システム)などの⽣産管理システムのデータを利⽤することで、⽣産ライン全体の設備の稼働・人の作業の進捗状況を収集・把握できる。 | 設備の稼働・人の作業の進捗状況を基に、各プロセスの完了予定時間を予測できる。設備と人の⾮稼動時間が発⽣する要因を分析できる。 | ⽣産ライン全体の⽣産完了予定時間が最短化されるよう、設備の稼動計画、段取り替え計画、人の作業計画を修正・最適化することで、設備・人の⾮稼動時間を最⼩化できる。 | ・素形材加工企業・設備・金型供給企業・組み立て企業 | ・生産 |
(2)人の作業の効率化、作業の削減・負担軽減 | HMI(モバイル端末、スマートグラスなど)・RFIDなどを活⽤することで、調達した資材や⽣産した製品の管理情報、⽣産情報、設備の稼動情報を迅速かつ簡易に⼊⼒・表⽰できる。設備にセンサを取り付けたり、人の作業状況(作業動線、作業時間、作業内容など)をセンシングすることで、稼働状況・作業状況を収集・把握できる。 | 作業の進捗状況に応じて、HMIに必要な情報や作業指⽰を予測して表⽰できる。収集したデータをロボットに学習させることで、人の⾏動を予測し、協調して作業できる。 | 情報の⼊⼒・表⽰の⾃動化による作業の短時間化や、適切な判断を⽀援する情報を提⽰することで、作業プロセスを最適化できる。人とスマートロボットによる協調した作業を最適化することで、人の作業の効率を向上できる。 | ・素形材加工企業・設備・金型供給企業・組み立て企業 | ・受注・調達・生産・物流・販売 |
(3)設備の故障に伴う稼動停止の削減 | 設備にセンサを取り付けてモニタリングすることで、設備の稼働状況を収集・監視できる。設備にセンサを取り付けてモニタリングすることで、設備の稼働状況を収集・監視できる。異常や故障が発⽣した際、人へ早期に通知できる。 | 収集したデータと設備異常とを関連付けて、設備の故障につながる兆候・条件を明らかにすることで、故障の発⽣時期を予測できる。過去の故障事例を分析することで、正確な原因究明や適切な対策の⽴案につながる知⾒を体系化できる。 | 設備の故障予測に基づき、予防保全することで、故障の発⽣を抑制し、想定外の稼動停⽌時間を削減・最⼩化できる。設備の故障が発⽣したときに、知⾒に基づいて原因究明・対策検討の判断を⽀援することで、復旧を早期化し、稼動停⽌時間を削減・最⼩化できる。 | ・素形材加工企業・設備・金型供給企業・組み立て企業 | ・⽣産 |
(1)設備・人の稼働率の向上
最初に、製造実行システム(MES)などの生産管理システムのデータを活用することで、生産ライン全体の設備の稼働状況と労働者の進捗状況をリアルタイムで収集・把握できる環境を整えることが必要です。
これにより、各工程の完了予定時間を予測し、設備と労働者の非稼働時間の要因を分析できるようになります。
最終的には、生産ライン全体の生産完了予定時間を最小化するために、設備の運用計画、設定変更計画、労働スケジュールを調整・最適化することで、設備と労働力の非稼働時間を最小限に抑える環境を整備することが重要です。
(2)人の作業の効率化、作業の削減・負担軽減
労働者の業務とプロセスの最適化に関しては、最初に、モバイル端末、スマートグラス、RFIDなどを活用して、資材調達情報、製品製造情報、設備の稼働情報などをスムーズに入力・表示できる環境を整備することが必要です。
また、作業進捗状況に基づいて、必要な情報や作業指示を予測的に表示できるようにすることが大切です。最終的には、情報入力と表示の自動化により、作業時間の短縮と適切な判断をサポートする情報の提供によって、業務プロセスを最適化することが重要です。
また、人間とロボットの協力による効率化に関して、設備にIoTセンサーを設置し、作業者の動線、作業時間、作業内容などの情報を収集することで、稼働状況と作業状況を収集・把握できる環境を整備する必要があります。次に、収集したデータをロボットに学習させ、人間の動きを予測し、協力して作業できるようにすることが大切です。
最終的には、人間とスマートロボットの協力作業を最適化することで、労働者の効率を向上させることが重要です。
(3)設備の故障に伴う稼動停止の削減
故障頻度を最小限に抑えるために、まず設備にIoTセンサーを設置し、設備の稼働状況をリアルタイムでモニタリングできるようにすることが必要です。
そして、収集したデータと設備の異常との関連を明らかにして、故障の兆候や条件を予測できるようにすることが大切です。最終的には、設備の故障予測に基づいて予防保全を実施し、故障発生を抑制し、予期せぬ停止時間を削減・最小限にするための環境を整備することが重要です。
また、迅速な復旧に向けて、設備にセンサーを設置し、設備の稼働状況をリアルタイムで収集・監視し、異常や故障が発生した場合には、従業員に自動的に通知する仕組みを導入することが必要です。
そして、過去の故障事例を分析して、正確な原因の特定や適切な対策の策定に貢献する知識を組織化することが大切です。最終的には、故障時には知識に基づいて原因特定と対策策定を支援することで、復旧を迅速化し、稼動停止時間を削減・最小限にする環境を整備することが重要です。
④製品化・量産化の期間短縮
4つ目の目的は、「製品化・量産化の期間短縮」です。
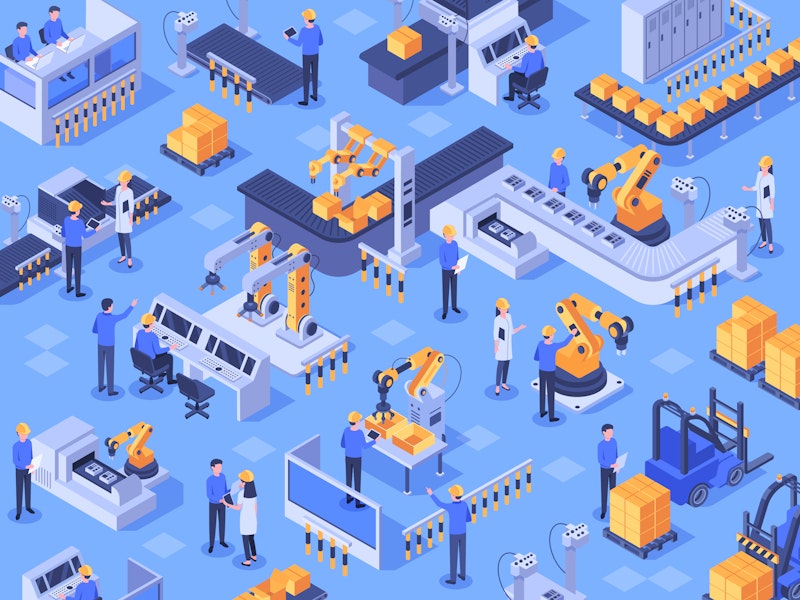
スマートファクトリー化の目的 | レベル1(データの収集・蓄積) | レベル2(データによる分析・予測) | レベル3(データによる制御・最適化) | 対象企業層 | スマート化の対象プロセス |
---|---|---|---|---|---|
(1)製品の開発・設計の自動化 | 設計事例を収集してデータベースとして蓄積することで、過去の事例を容易に参照できる。解析・シミュレーションソフトウェアを利⽤することで、構造等を解析できる。 | 過去の設計事例や、解析・シミュレーションソフトウェアなどによって分析することで、設計仕様を満たし、かつ、⽣産しやすい形状・構造等を知⾒としてモデル化できる。 | 構築した設計改善モデルを⽤いて、製品設計を⾃動化することで、製品開発・設計期間を短縮できる。 | ・素形材加工企業・設備・金型供給企業・組み立て企業 | ・製品企画、開発・設計 |
(2)仕様変更への対応の迅速化 | E-BOM(設計部品表)やM-BOM(製造部品表)などを利⽤することで、部品の詳細情報を容易に表⽰・確認できる。 | E-BOMやM-BOMなどをデータ連携することで、開発、設計、⽣産のデータを⼀元的に管理できる。仕様変更となった場合、影響範囲と影響度を分析できる。 | 仕様変更となった場合、統合BOMを通じて、開発、設計、⽣産⼯程のデータを連動させて反映することで、仕様変更の対応時間を最⼩化できる。 | ・素形材加工企業・設備・金型供給企業・組み立て企業 | ・受注・調達・生産 |
(3)生産ラインの設計・構築の短縮化 | ⽣産ラインシミュレータなどを利⽤することで、サイバー上で⽣産ラインを設計できる。 | ⽣産ラインシミュレータなどを利⽤することで、⽣産ラインのレイアウト、⽣産能⼒、作業⼯程、搬送ルート、投資コストなどを事前に評価・検証できる。 | サイバー上で⽣産ラインを設計し最適化した上で、実世界の⽣産現場へ実装することで、構築時の試⾏錯誤を削減し⽣産ライン構築期間を短縮できる。 | ・素形材加工企業・設備・金型供給企業・組み立て企業 | ・⽣産 |
(1)製品の開発・設計の自動化
過去の設計事例をデータベースに収集し、容易にアクセスできるようにします。これにより、解析とシミュレーションソフトウェアを活用して、製品の構造などを詳細に分析できます。
また、過去の設計事例と解析・シミュレーションソフトウェアの活用により、製品の設計仕様を満たし、かつ生産が効率的な形状や構造などをモデル化できます。最後に、構築した設計改善モデルを活用して、製品の設計を自動化することで、製品開発と設計の期間を短縮することができます。
(2)仕様変更への対応の迅速化
E-BOM(設計部品表)やM-BOM(製造部品表)などを活用して、部品の詳細情報を簡単に表示および確認できます。さらに、E-BOMやM-BOMなどをデータ連携し、開発、設計、生産のデータを一元的に管理することができます。
仕様変更が発生した場合、影響範囲と影響度を分析できます。仕様変更が生じた場合、統合BOMを通じて、開発、設計、生産プロセスのデータを統合させて反映することで、仕様変更に対する対応時間を最小限に抑えることができます。
(3)生産ラインの設計・構築の短縮化
生産ラインシミュレータなどを活用して、仮想の環境で生産ラインを設計することが可能です。また、生産ラインシミュレータなどを使用して、生産ラインのレイアウト、生産能力、作業プロセス、搬送経路、投資コストなどを事前に評価および検証できます。
最後に、仮想環境で生産ラインを設計し、最適化した後、実際の生産現場に導入することで、構築時の試行錯誤を削減し、生産ラインの設計と構築期間を短縮することができます。
⑤人材不足・育成への対応
5つ目の目的は、「人材不足・育成への対応」です。
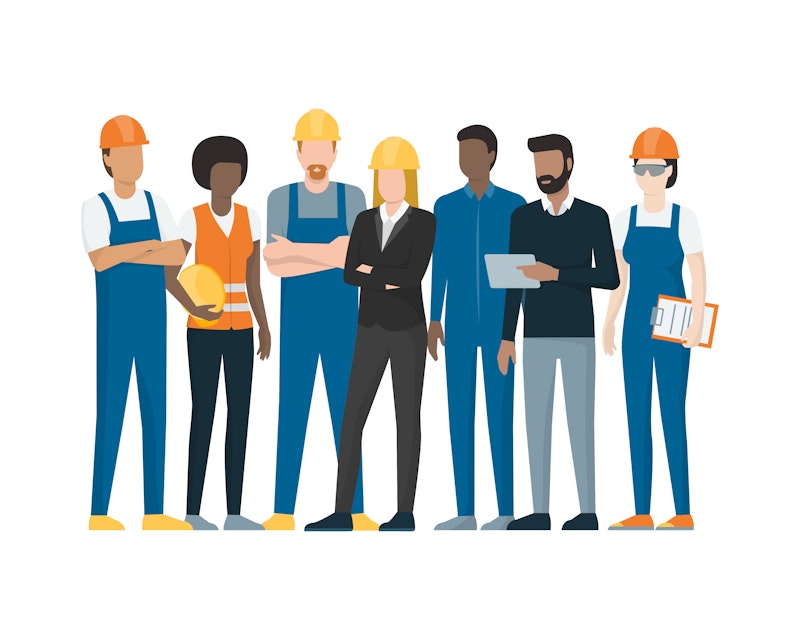
スマートファクトリー化の目的 | レベル1(データの収集・蓄積) | レベル2(データによる分析・予測) | レベル3(データによる制御・最適化) | 対象企業層 | スマート化の対象プロセス |
---|---|---|---|---|---|
(1)多様な人材の活用 | 各従業員の作業熟練度、知識、⾝体能⼒、使⽤⾔語などを、データベースとして蓄積することで、各従業員の特性情報を利⽤できる。 | - | HMD(ヘッドマウントディスプレイ)や⾳声認識機器などのウェアラブルデバイス、パワーアシストスーツ、⽣体センサなどを活⽤し、人の能⼒を拡⼤することで、特性が異なる多様な⼈材を活⽤できる。 | ・素形材加工企業・設備・金型供給企業・組み立て企業 | ・生産 |
(2)技能の継承 | 熟練技能者の技能(段取り調整⼒、状況判断⼒、⼿わざ、トラブル対応⼒など)をセンシングすることで、データベースとして蓄積できる。 | 収集したデータを分析し、その他の作業者と⽐べて熟練技能者が優れている点を明らかにすることで、技能・ノウハウ・知⾒を体系化できる。 | 体系化した技能・ノウハウ・知⾒を国内外の拠点へ共有することで、それらを継承し、人の能⼒を向上できる。それらをスマートロボットに学習させることで、人を代替できる。 | ・素形材加工企業・設備・金型供給企業・組み立て企業 | ・生産 |
(1)多様な人材の活用
まず、各従業員の作業熟練度、知識、体力、使用言語などの特性情報をデータベースに蓄積し、各従業員の個性を活用できるように整備する必要があります。
最終的には、HMD(ヘッドマウントディスプレイ)や音声認識機器などのウェアラブルデバイス、パワーアシストスーツ、生体センサなどを活用して、人間の能力を拡大し、異なる特性を持つ多様な人材を効果的に活用できる仕組みを構築することが重要です。
(2)技能の継承
最初に、熟練技能者のスキル(段取り調整能力、状況判断力、手仕事、トラブル対応スキルなど)をセンシングし、データベースに蓄積する必要があります。次に、収集したデータを分析し、他の作業者と比較して熟練技能者が優れている点を明らかにし、技能、ノウハウ、知識を体系化することが重要です。
最終的には、体系化された技能、ノウハウ、知識を国内外の拠点で共有し、これらを継承し、人の能力を向上させます。さらに、これらをスマートロボットに学習させ、人間を代替できる仕組みを構築することが重要です。
⑥新たな付加価値の提供・提供価値の向上
6つ目の目的は、「新たな付加価値の提供・提供価値の向上」です。
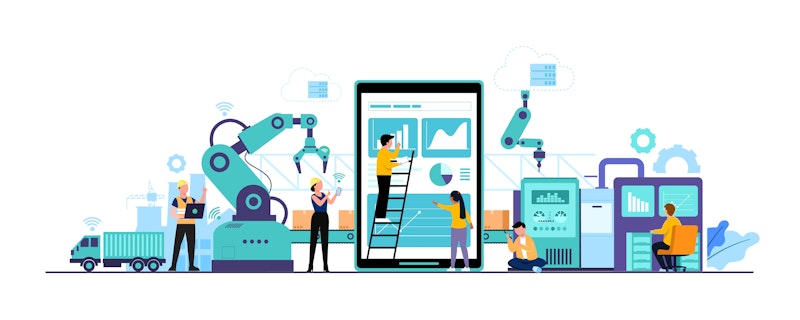
スマートファクトリー化の目的 | レベル1(データの収集・蓄積) | レベル2(データによる分析・予測) | レベル3(データによる制御・最適化) | 対象企業層 | スマート化の対象プロセス |
---|---|---|---|---|---|
(1)多用なニーズへの対応力の向上 | 各製品に共通する部分を定義して、製品の構造、設計・⽣産プロセス、加⼯基準などを共通化することで、共通モジュールと個別モジュールの組み合わせによるフレキシブルな⽣産体制を構築できる。ERP(統合業務管理システム)、MES(製造実⾏システム)、SCM(サプライチェーンマネジメントシステム)などのデータを利⽤することで、受注、調達、⽣産、物流、販売などの計画・実績データを、容易に表⽰・確認できる。 | 調達・⽣産・販売などの社内関係部⾨間でデータ連携することで、調達計画・⽣産計画・物流計画などを情報共有できる。受注状況、販売状況などを分析することで、需要を予測できる。社内関係部⾨やサプライチェーン上の企業間でデータ連携することで、調達計画・⽣産計画・物流計画などを情報共有できる。 | 設備・ヒトへの作業指⽰・部品供給や段取り替えの計画策定を⾃動化・最適化することで、個別のニーズにあわせて多品種の製品をフレキシブルに⽣産できる。サプライチェーン全体で、⽣産計画・物流計画などを最適化することで、顧客ニーズにあわせてオンデマンドに製品・サービスを提供できる。 | ・組み立て企業 | ・受注・調達・⽣産・物流・販売 |
(2)提供可能な加工技術の拡大 | MES(製造実⾏システム)などの⽣産管理システムのデータを利⽤することで、⽣産の進捗状況を収集・把握できる。 | 共同受注を⾏う企業間でデータ連携することで、⽣産計画・進捗状況などを情報共有できる。 | 各企業における加⼯時間・加⼯ロット単位などの違いを考慮して、全体で、⽣産計画・物流計画などを最適化することで、共同受注⽣産体制を構築し、様々な加⼯技術を提供できる。 | ・素形材加工企業 | ・受注・調達・⽣産 |
(3)新たな製品・サービスの提供 | 製品にセンサ・通信機能を 搭載することで、製品の使⽤状況や使⽤環境のデータを収集・把握できる。製品に組み込まれたセンサなどを利⽤したり、製品にセンサ・通信機能を搭載することで、製品の使⽤状況、使⽤環境のデータ、製品の制御データを収集・把握できる。 | 収集したデータを分析し、ユーザを⾏動観察する(⼈間⼯学、⼼理学などの観点から分析する)ことで、⾮顕在ニーズを把握できる。収集したデータを分析し、製品の利⽤改善・予防保全につながる知⾒や、別⽤途への製品稼動情報の利⽤による新たな付加価値提供につながる知⾒を獲得できる。 | 把握したニーズを実現する製品・機能・サービスを先回りして企画・提案できる。獲得した知⾒を活⽤することで、製品に関連した新たなサービス・アフターサービスを提供できる。 | ・設備・⾦型供給企業・組み⽴て企業 | ・製品企画、開発・設計・製品稼働、サービス提供 | (4)製品の性能・機能の向上 | 製品に組み込まれたセンサなどを利⽤したり、製品にセンサ・通信機能を搭載することで、製品の使⽤状況、使⽤環境のデータ、製品の制御データを収集・把握できる。製品に通信機能を搭載する ことで、ユーザが使⽤している製品の状態を収集・把握できる。 | 収集したデータを分析することで、ユーザにおける製品の使⽤⽅法の傾向を把握できる。 | ユーザにおける製品の使⽤⽅法の傾向にあわせて、製品の制御設定値を最適化することで、製品の性能を最⼤化・カスタマイズ化できる。通信機能を通じて、ソフトウェアを遠隔アップデートすることで、製品に新規機能を追加できる。 | ・設備・⾦型供給企業・組み⽴て企業 | ・製品稼働、サービス提供 |
(1)多用なニーズへの対応力の向上
多品種の製品を個別のニーズに合わせて提供する側面では、まず、各製品に共通する要素を定義し、製品の構造、設計、生産プロセス、加工基準などを共通化することで、共通モジュールと個別モジュールを組み合わせて柔軟な生産体制を構築する必要があります。
次に、調達、生産、販売などの社内関連部門間でデータ連携を行い、調達計画、生産計画、物流計画などを情報共有できるようにすることが重要です。
最終的には、設備の稼働計画、作業指示、部品供給、段取りの計画を自動化および最適化することで、個別のニーズに合わせて多品種の製品を柔軟に生産できるようになります。
顧客のオンデマンドな製品とサービスの提供に関しては、最初にERP(統合業務管理システム)、MES(製造実行システム)、SCM(サプライチェーンマネジメントシステム)などのデータを活用して、受注、調達、生産、物流、販売などの計画と実績データを簡単に表示および確認できるようにすることが必要です。
次に、受注状況や販売状況を分析することで、需要を予測できます。社内の関連部門およびサプライチェーン上の他社とデータ連携を行い、調達計画、生産計画、物流計画などを情報共有できるようにします。
最終的に、サプライチェーン全体で生産計画、物流計画などを最適化することで、顧客のニーズに合わせてオンデマンドで製品とサービスを提供できるようになります。
(2)提供可能な加工技術の拡大
加工技術の提供という面では、まず、MES(製造実行システム)などの生産管理システムのデータを利用して、生産の進捗状況を収集および把握できるようにすることが必要です。
次に、共同受注を行う企業間でデータ連携を行い、生産計画および進捗状況などを情報共有できるようにします。
最終的には、各企業の加工時間および加工ロット単位などの違いを考慮して、全体として生産計画および物流計画を最適化し、共同受注生産体制を構築し、さまざまな加工技術を提供できるようになります。
(3)新たな製品・サービスの提供
新製品を先取りした企画と提案に関しては、まず、製品にセンサや通信機能を組み込むことで、製品の使用状況や使用環境のデータを収集および把握できるようにすることが必要です。
次に、収集したデータを分析し、ユーザーの行動観察(人間工学、心理学などの観点から分析)を行うことで、潜在的なニーズを把握できるようにします。
最終的には、把握したニーズに合った製品、機能、サービスを先取りして企画および提案できるようになります。
新しいサービスの提供に関しては、最初に製品に組み込まれたセンサなどを活用したり、製品にセンサや通信機能を組み込むことで、製品の使用状況、使用環境のデータ、製品の制御データを収集および把握できるようにすることが必要です。
そして最終的には、収集したデータを分析し、製品の利用向上と予防保全につながる洞察や、別の用途での製品活用情報を提供することで、新しいサービスとアフターサービスを提供できるようになります。
(4)製品の性能・機能の向上
製品の性能を最大化し、カスタマイズする側面では、最初に製品に組み込まれたセンサや通信機能を活用することで、製品の使用状況や使用環境のデータ、製品の制御データを収集および把握できるようにすることが必要です。
次に、収集したデータを分析することで、ユーザーの製品使用方法の傾向を理解できるようになります。
最終的には、ユーザーの製品使用方法に合わせて、製品の制御設定を最適化することで、製品の性能を最大化し、カスタマイズできるようになります。
新機能の追加に関しては、製品に通信機能を組み込むことで、ユーザーが使用している製品の状態を収集および把握できるようにすることが必要です。
そして最終的には、通信機能を介して、ソフトウェアを遠隔でアップデートすることで、製品に新しい機能を追加できるようになります。
⑦その他
7つ目の目的は、上記で紹介してきた6つ以外の「その他」です。
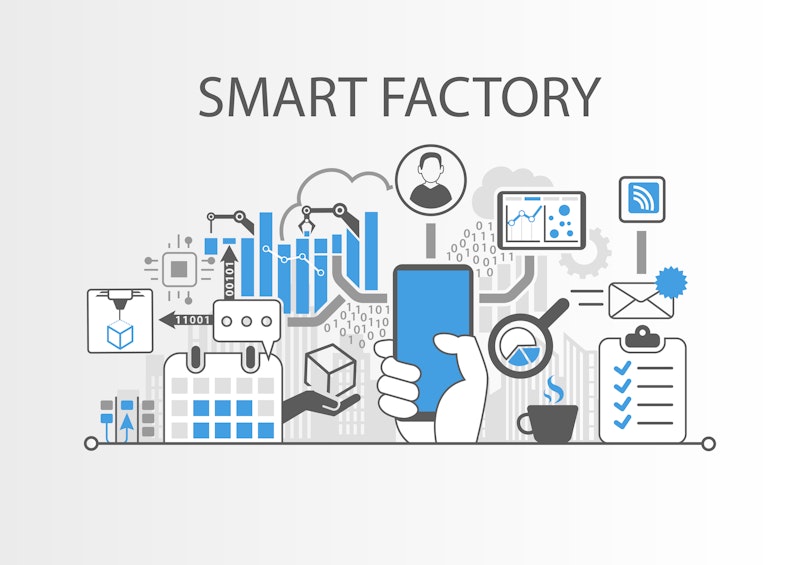
スマートファクトリー化の目的 | レベル1(データの収集・蓄積) | レベル2(データによる分析・予測) | レベル3(データによる制御・最適化) | 対象企業層 | スマート化の対象プロセス |
---|---|---|---|---|---|
(1)リスク管理の強化 | 製品にRFIDや通信機能を搭載し、加⼯・組⽴・検査・出荷のデータを蓄積することで、製品個体毎の品質を証明できる。 | 製品に不具合が発⽣したときに、製品や資材に蓄積されたデータを分析することで、不具合の原因の特定を早期化できる。 | 製品に不具合が発⽣したときに、通信機能を通じて、製品を使⽤しているユーザを把握し、対策を講ずることで、影響範囲を最⼩化できる。 | ・組み立て企業 | ・製品稼働、サービス提供 |
(1)リスク管理の強化
リスク管理を強化するために、最初に製品にRFIDや通信機能を組み込み、加工、組み立て、検査、出荷に関するデータを蓄積し、各製品個体の品質を確認できるようにする必要があります。
次に、製品に不具合が発生した場合、製品や資材に蓄積されたデータを分析して、不具合の原因を早期に特定できるようにすることが重要です。
最終的に、製品に問題が発生した場合、通信機能を介して製品の使用者を特定し、適切な対策を講じることで、影響範囲を最小限に抑えることができるようになります。
スマートファクトリーのメリット
次に、スマートファクトリーの導入メリットについて紹介します。スマートファクトリー導入のメリットについては、目的部分と被る部分はありますが、大きく分けて2つのメリットがあります。
①製造に関わるあらゆるデータの見える化
1つ目のメリットは、「製造に関わるあらゆるデータの見える化」です。これまで、工場現場の熟練技術者による経験や勘によって、見える化できていなかったデータや、工場内のありとあらゆるデータをスマートファクトリー導入で見える化することにより、これまでよりもさらに効率を上げ、生産性を高めることが期待できます。
②リソースの省力化と最適化
1つ目のメリットは、「リソースの省力化と最適化」です。製造業が抱える3つの課題でも言及したように、日本の製造業では、年々「労働力の不足」が続いていますが、スマートファクトリー導入により、余分な人の作業工程を減らすことで省力化を実現し、様々な製造工程で最適化ができるようになります。
スマートファクトリー導入の課題
スマートファクトリー導入の課題については、大きく分けて2つあります。
①DX(デジタル)人材の不足
スマートファクトリー導入の1つ目の課題が、「DX(デジタル)人材の不足」です。スマートファクトリーの前提となるデジタル技術の導入や活用、運用に対して、知見のあるDX人材は、日本のみならず、世界中で様々な業界が人材獲得競争を繰り広げています。しかし、スマートファクトリーを成功に導くDX人材は、その数が少ないため、このDX人材を育てたり、獲得したりするには、多少の時間がかかってしまいます。
「DX人材」について詳しく知りたい方は、こちらの記事もご覧ください。
『DX成功に欠かせないDX人材の職種やスキルなどを徹底解説します!』
②セキュリティの強化
スマートファクトリー導入の1つ目の課題が、「セキュリティの強化」です。スマートファクトリーでは、IoTやM2M、AI、ICT、ITなど様々なデバイスや人の情報を扱うようになるため、これまで行なってきたようなセキュリティ対策だけでは、セキュリティ対策としては不十分な状況になります。
「IoTセキュリティ」について詳しく知りたい方は、こちらの記事もご覧ください。
『IoTセキュリティとは?IoTセキュリティの問題や課題からIoTセキュリティ対策の必要性まで徹底紹介!』
スマートファクトリーの普及率と市場規模
次に紹介するのは、スマートファクトリーの普及率と市場規模についてです。
スマートファクトリーの普及率
スマートファクトリーの普及率について、経済産業省が2020年に公表した『2020年版ものづくり白書』によると、「デジタル技術を活用している」と回答した企業は49%である一方で、「未活用(活用を検討中、活用していない、無回答)」と回答した企業も51%となり、製造業では、二極化が進んでいます。
さらに、大企業と中小企業で分けて見てみると中小企業の方が大企業に比べて、デジタル技術を活用を推進できていません。
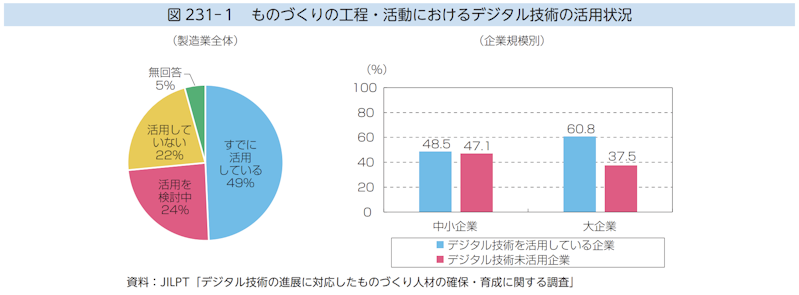
さらに、企業別と、工程・活動別では、下記のようにデジタル技術の活用に違いがあります。
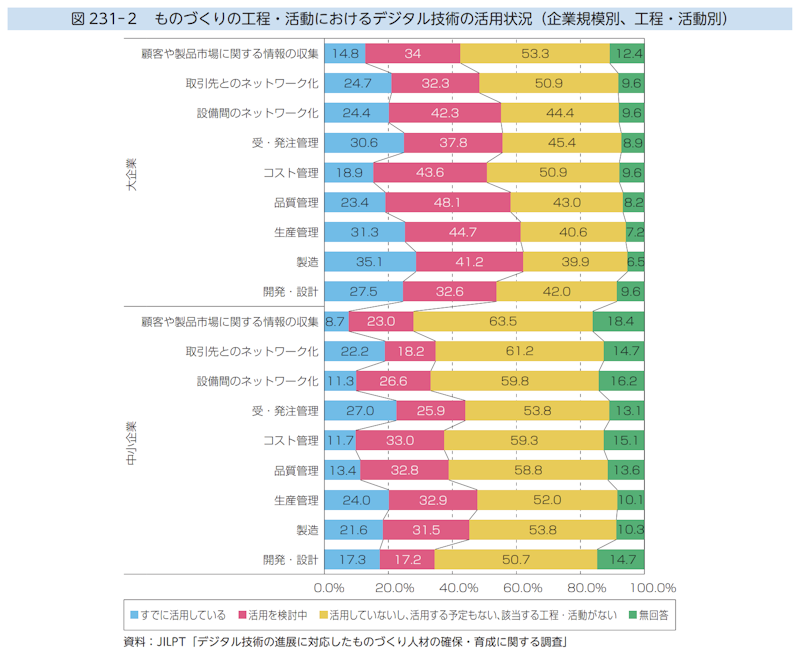
最後に、製造業の中でも細分化して、細かく見てみると下記のようにデジタル技術の活用に違いがあります。
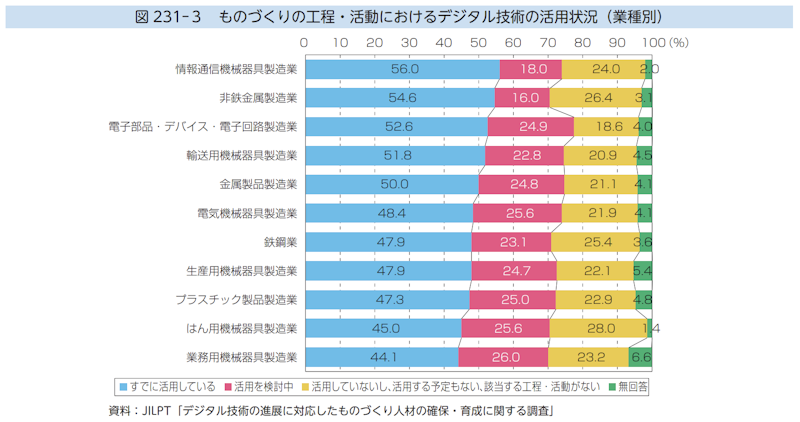
(参考)2020年版ものづくり白書(PDF版)|経済産業省
スマートファクトリーの市場規模
スマートファクトリーの市場規模は、富士経済が公表した『NEXT FACTORY関連市場の実態と将来展望 2020』の中で「スマートファクトリー関連システム・製品の世界市場」としてまとめて公表しています。
それによると、2020年のスマートファクトリーの世界市場規模は、2兆4,142億円の見込みで、2025年には、5兆5,446億円になる予測が立てられています。
・2020年 2兆4,142億円(見込み)
・2025年 5兆5,446億円(予測)
(参考)スマートファクトリー関連システム・製品の世界市場を調査|富士経済グループ
スマートファクトリー事例4選
ここからは、スマートファクトリー事例を4つ紹介します。
【日工】コンクリートプラントのスマートファクトリー化
土木用プラントで国内シェアNo.1の日工株式会社は、コンクリートプラントに導入可能な国内初となる画像認識AIによる骨材判別システム「骨材判別AI」を開発し、22年3月に1号機の本格運用を開始しコンクリートプラントのスマートファクトリー化を推進することを2022年2月28日に公表しました。
(参考)日工がプラントに導入可能なAIシステムを開発 コンクリートプラントのスマートファクトリー化を推進!“国内初”となる画像認識AIによる骨材判別システム『骨材判別AI』の本格運用開始|PRTIMES
【武蔵精密工業】山梨スマートファクトリー
武蔵精密工業株式会社のグループ会社である武蔵エナジーソリューションズ株式会社では、山梨県南アルプス市に自然豊かな同市の環境に調和したスマートファクトリー設立に向けて新たに土地を取得することを2022年3月16日に公表しました。
(参考)「山梨スマートファクトリー」設立に向けて土地を取得|PRTIMES
【日立ハイテク】スマートファクトリー「マリンサイト」
株式会社日立ハイテクは、茨城県ひたちなか市に2019年11月より建設を進めていた、半導体製造装置および解析装置の設計・開発・製造を担う新工場「マリンサイト」が竣工したと公表しました。
(参考)最新鋭の設備と環境に配慮した運営で生産性の向上と脱炭素を両立するスマートファクトリー「マリンサイト」竣工|PRTIMES
【花王】「豊橋コネクテッド・フレキシブル・ファクトリー」
花王株式会社は、「人と環境にやさしく、安定して生活者・顧客の皆さまに製品をお届けできる、柔軟で効率的な生産体制と新たな物流モデル」の構築を目指し、スキンケアやヘルスケア製品を中心に生産する豊橋工場の生産・物流機能一体型サプライチェーン拠点(「豊橋コネクテッド・フレキシブル・ファクトリー」)へと変革すると2022年3月3日に公表しました。
(参考)豊橋工場に柔軟で効率的な生産体制と新たな物流モデルを構築|PRTIMES
スマートファクトリーを学びたい人におすすめの書籍・本4選
ここでは、スマートファクトリーを学びたい人におすすめの書籍や本を4つ紹介します。
イラスト図解 スマート工場のしくみ IoT、AI、RPAで変わるモノづくり
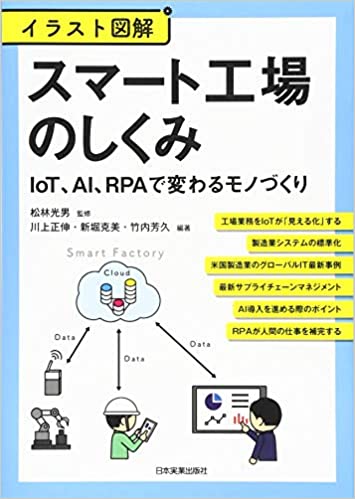
おすすめポイント
激化しているグローバル競争の中で、「スマート工場」というDX戦略で勝つために書かれた一冊です。基本的なスマート工場の仕組みや実際の業務工程を支える技術の説明などがわかるため、工場業務に関わるすべての人におすすめです。
こんな方におすすめ
・製造業界の経営者
・製造業界の従業員
・製造業界のDX担当者
書籍名
イラスト図解 スマート工場のしくみ IoT、AI、RPAで変わるモノづくり
目次
・はじめに
・1章 工場経営とモノづくりのしくみ
・2章 工場の業務を支える基準情報と情報システム
・3章 最新サプライチェーンのすべて
・4章 モノづくりを支える大切な機能と世界の最新事情
・5章 工場におけるIoTの活用
・6章 工場におけるAI、ビッグデータ、RPAの活用
・7章 製造業が勝ち残るためのグローバルIT戦略
発行日
2018年8月30日
著者・編集
川上 正伸、竹内 芳久、新堀 克美
監修
松林 光男
Amazonリンク
https://www.amazon.co.jp/dp/4534056125/
小説 第4次産業革命 日本の製造業を救え!
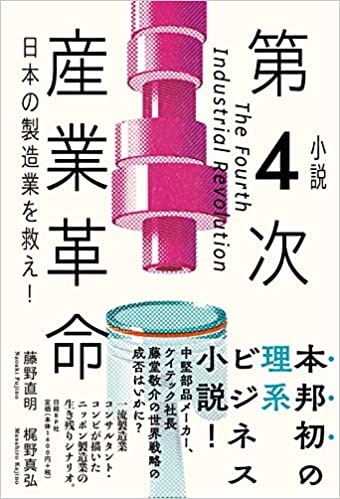
おすすめポイント
本書はビジネス書ではなく小説という形式で、製造業のDXの本質やインダストリー4.0をストーリー形式で理解できる一冊です。「倍返しだ!」で有名な池井戸潤氏の作風に似ているところがあり、とても読み進めやすい小説です。製造業界に携わる方のみでなく、すべてのビジネスパーソンにおすすめです。
こんな方におすすめ
・製造業界の経営者
・製造業界の従業員
・製造業界のDX担当者
書籍名
小説 第4次産業革命 日本の製造業を救え!
目次
・第1章 顧客が消える!
・第2章 ドイツからの商談
・第3章 新日独同盟論
・第4章 ケイテック改造計画
・第5章 スマート工場・プラットフォーム企業への飛躍
・第6章 モデルベース開発
・第7章 遠隔工場プラン
・終章 フォースサポート、東証マザーズ上場
発行日
2019年4月18日
著者
藤野 直明、梶野 真弘
Amazonリンク
https://www.amazon.co.jp/dp/4822289656/
改革・改善のための戦略デザイン 製造業DX
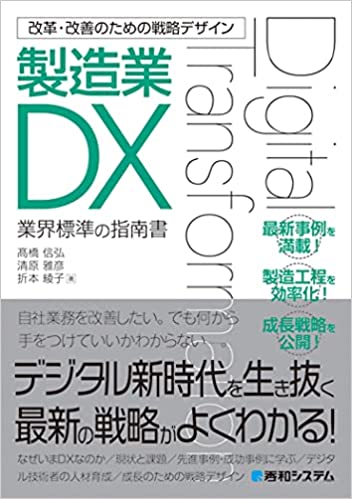
おすすめポイント
製造業におけるDXについて事例を具体的に解説した業界標準の指南書です。製造業DXの現状と課題、「古い企業文化が邪魔をする」「DXを導入してもすぐに利益が出ない」などの最新事例、人材育成、戦略デザインなどが満載です。
こんな方におすすめ
・製造業界の経営者
・製造業界の従業員
・製造業界のDX担当者
書籍名
改革・改善のための戦略デザイン 製造業DX
目次
・1章 なぜいまDXなのか
・2章 製造業DXの現状と課題
・3章 先進事例・成功事例に学ぶ製造業のDX
・4章 成功するソフトウェアのデジタル技術者の人材育成に学ぶ
・5章 成長のための戦略デザイン
発行日
2021年11月26日
著者
高橋信弘、清原雅彦、折本綾子
Amazonリンク
https://www.amazon.co.jp/dp/4798065277/
図解入門ビジネス 最新生産工場のDXがよ~くわかる本
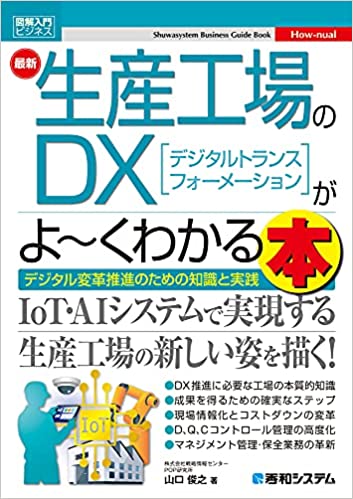
おすすめポイント
本書は、製造現場のDXに必要な工場の本質的な知識を図表を使ってわかりやすく解説した入門書です。
こんな方におすすめ
・製造業界の経営者
・製造業界の従業員
・製造業界のDX担当者
書籍名
図解入門ビジネス 最新生産工場のDXがよ~くわかる本
目次
・第1章 工場の本質的知識~DX推進のための知識①
・第2章 コントロール管理の知識~DX推進のための知識②
・第3章 マネジメント管理の知識~DX推進のための知識③
・第4章 確かなDXの進め方~DX推進のための知識④
・第5章 製造現場の情報化変革~DX化のテーマ①
・第6章 コストダウンと改善の変革~DX化のテーマ②
・第7章 D、Q、C管理の高度化~DX化のテーマ③
・第8章 マネジメント管理の革新~DX化のテーマ④
・第9章 保全業務の変革~DX化のテーマ⑤
発行日
2021年7月29日
著者
山口俊之
Amazonリンク
https://www.amazon.co.jp/dp/4798064432/

IoTBiz編集部
2015年から通信・SIM・IoT関連の事業を手掛けるDXHUB株式会社のビジネスを加速させるIoTメディア「IoTBiz」編集部です。
関連記事
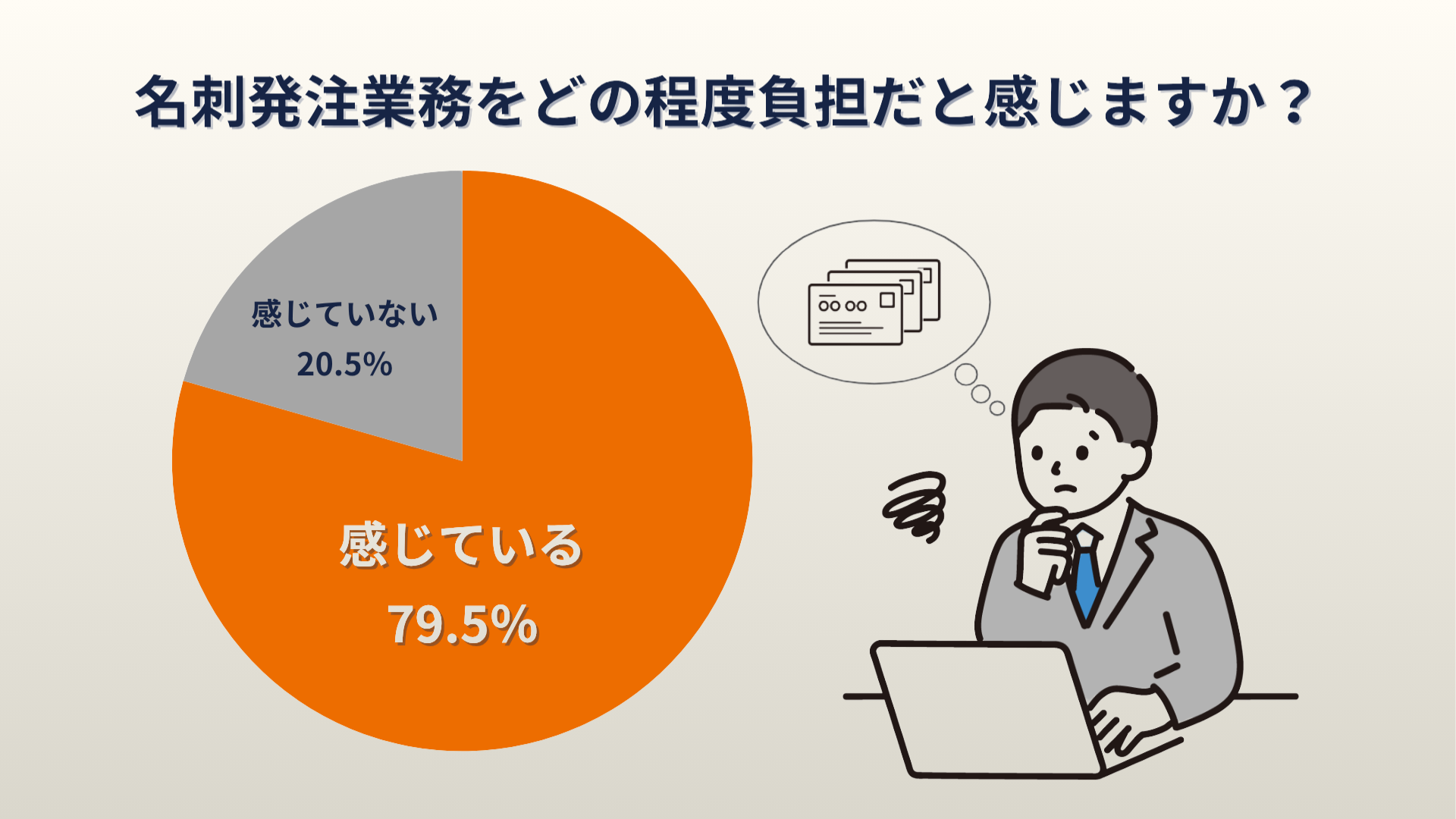
ニュース
DX
この記事では、株式会社オンデオマが実施した、「名刺作成における非効率とDX化の導入障壁」に関する調査について紹介しています。
2025-08-07
4min
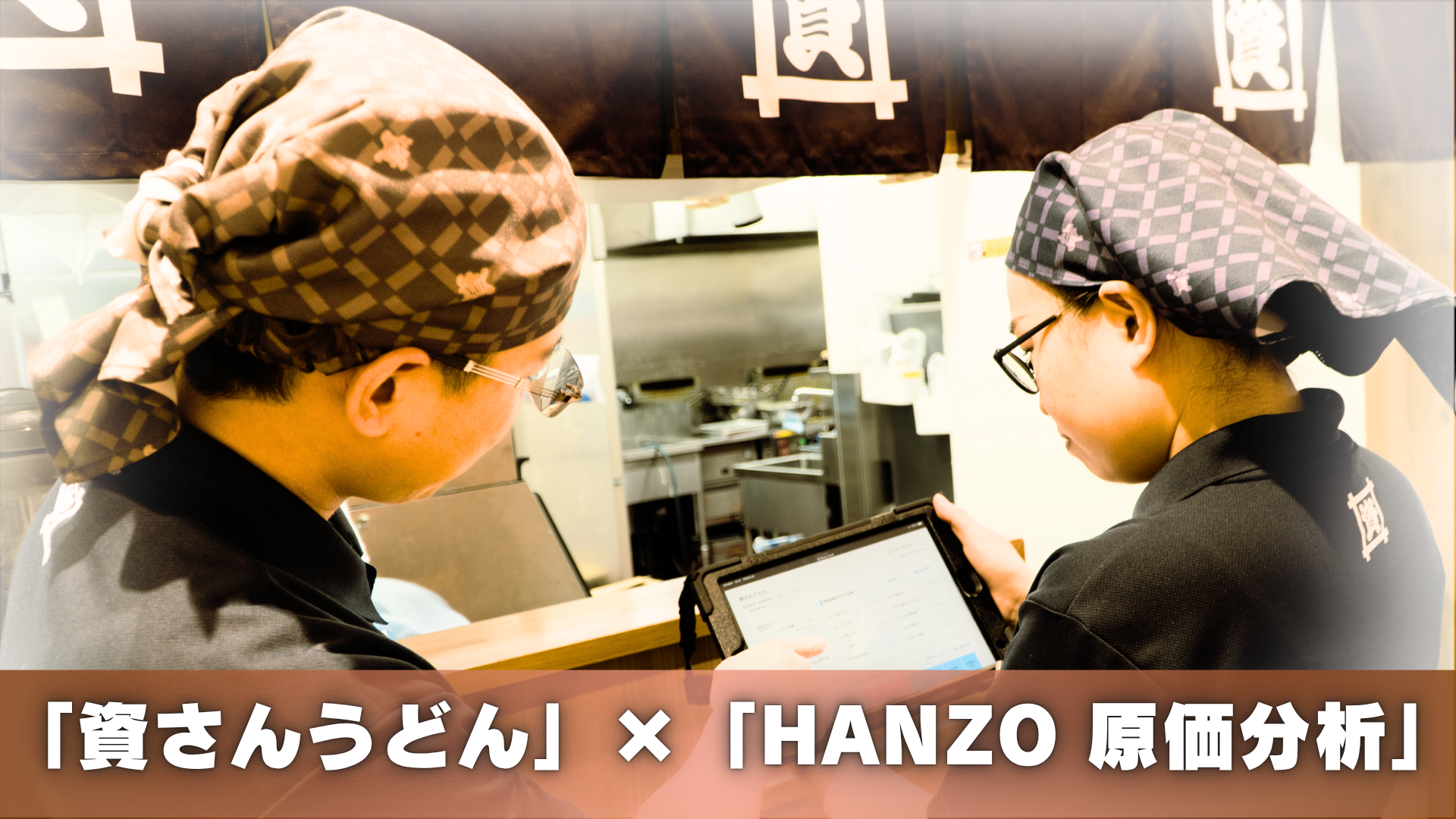
ニュース
スマート物流
IoT
この記事では、「資さんうどん」の株式会社資さんが、株式会社Goalsのサービス「HANZO 原価分析」を導入開始したことについて紹介しています。
2025-08-07
1min
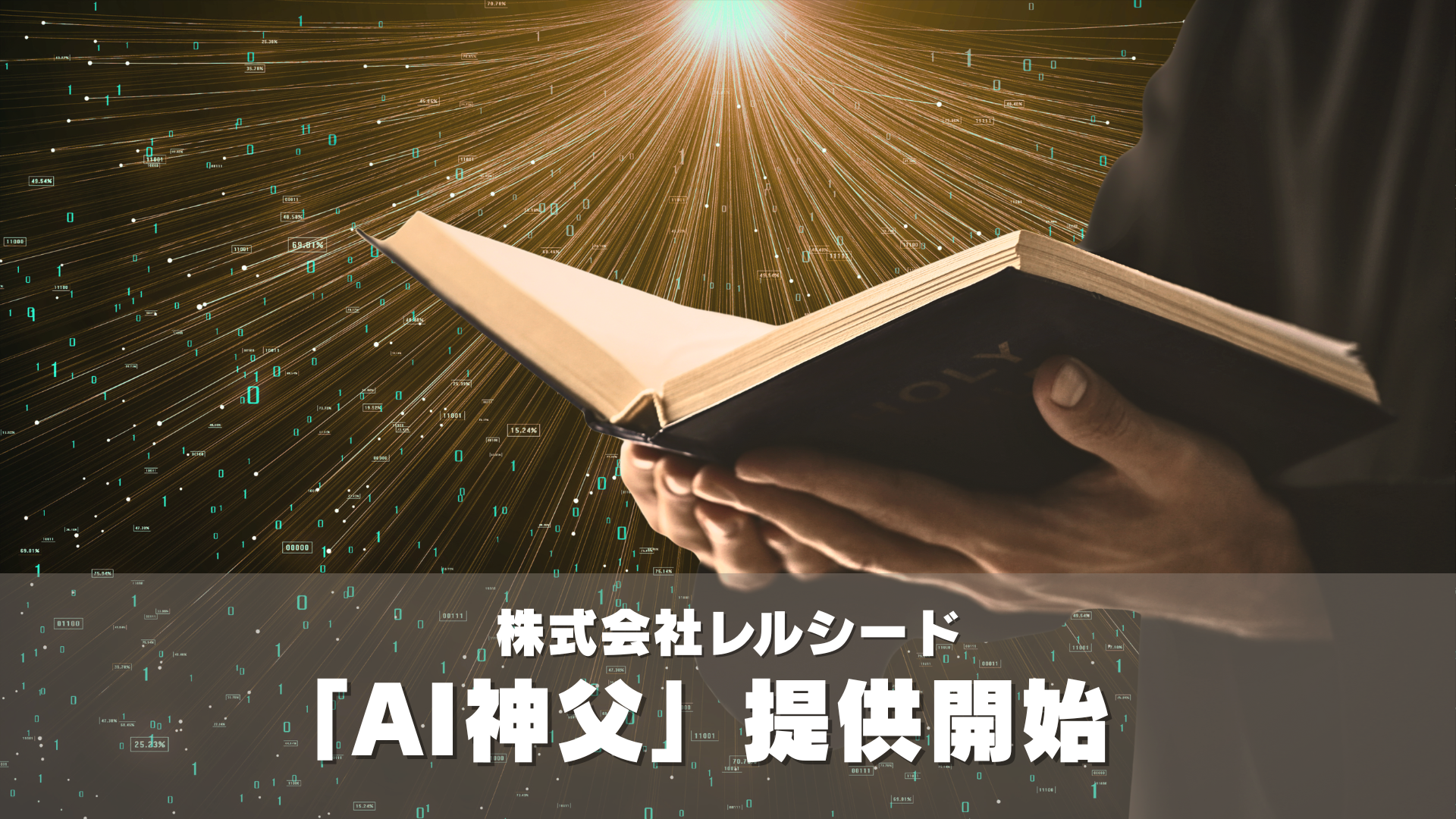
ニュース
AI
DX
この記事では、2025年7月22日から株式会社レルシードが提供開始した、対話型信仰支援AI「AI神父」について紹介しています。
2025-08-07
1min